-
Open the CATProcess containing the
Shell.CATProduct.
-
Identify the shapes along the shell in the
Product List.
-
Select Profile Bending Operation
.
-
Select BottShell_TStf_009.11
in the ProductList of the PPR tree.
The Profile Bending Operation dialog box appears:
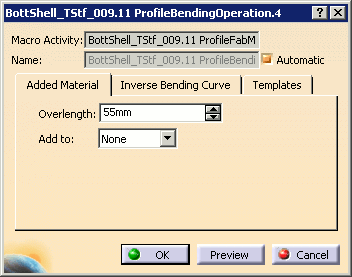 Inverse bending curves are previewed in the
geometry area:
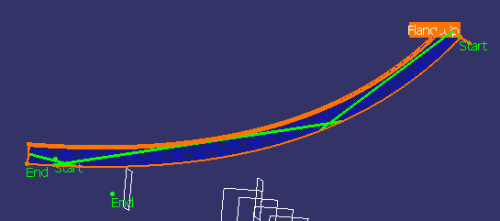 |
-
Define the amount of stock to add to the
shape before cutting and bending in the Overlength box, and specify to
which end or ends of the shape in the Add to list.
You can apply stock to both ends, one end or no end.
Note: Start and End are indicated in the geometry area to help you
identify shape ends.
Specify Inverse Bending Curves
|
-
Select the Inverse Bending Curve tab.
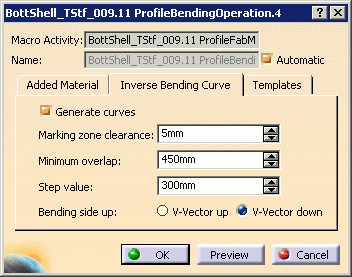
-
Specify whether or not you want to generate
inverse bending curves.
By default, these curves are generated. Leave this check box selected.
Note: Inverse bending curves can be generated automatically when
building the operation list (see
Tools > Options > Digital Process for Manufacturing > DPM - Structure
Lofting or
DPM - Structure Manufacturing Preparation > Activities).
-
Enter values for the marking zone clearance,
minimum overlap and step value, and identify the bending side up.
Marking zone clearance: specifies a clearance zone in
which inverse bending curves will not be generated.
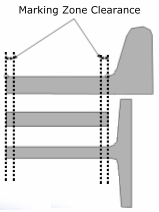 |
Minimum overlap: specifies the minimum distance between
the ends of inverse bending curves.
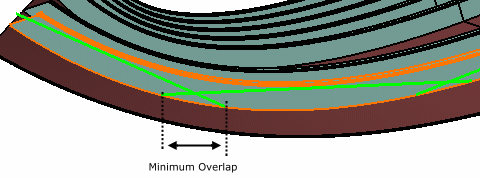 |
Step value: defines the work lines spaced along the
neutral axis that are used to extract inverse bending curve data.
This is an attribute on the inverse bending curve item. |
Bending side up: identifies the side to mark. The side
is determined with respect to the local u- and v-axes of the shape
cross-section. The v-vector orients the local v-axis.
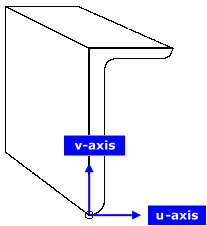 |
-
Select the Templates tab.
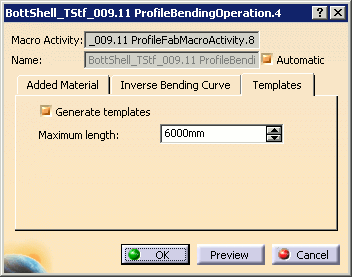
-
Specify whether or not you want to generate
templates.
By default, templates are generated. Leave this check box selected.
-
Enter the maximum length for the template.
This value is used to determine whether to generate more than one
template. If the length along the neutral axis is greater than the
maximum length entered, more than one template is generated.
-
Click OK when done.
Inverse bending curves are created on the profile
web as defined in the dialog box.
Any overlength specified is also created. |
 |
Templates are resources and are stored in a CATPart under the
ResourcesList node in the PPR tree, with one body per template.
This body contains the projected web surface with any openings and
endcuts. Templates are also identified under the Resources node of
the appropriate operation.
 |
-
Re-edit the operation to visualize the
projected web surface in the geometry area.
Note: You may need to rotate the sample to visualize the surface.
-
Open the template under the Resources node
in a new window.
In the example below, two templates have been generated for this shape: the length
along the neutral axis was greater than the maximum length of 6000mm
entered in the Profile Bending Operation dialog box.
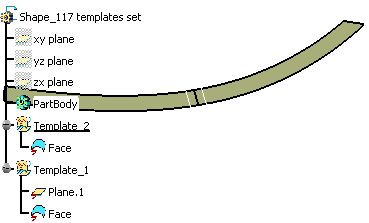
-
Close the window.
Update and View the IPM Part
|
-
Update the
in-process model (using the IPM Update command).
-
View the IPM part:
Note that the IPM part contains all the necessary features for the
downstream bending operation: inverse bending curves and any stock or
overlength specified.
-
Edit the profile bending operation and change
inverse bending curve specifications, then update the in-process model
and view the IPM part again.