 |
This task shows you how add a stagger origin. In the manufacturing
process of composite part, it is important to avoid, or at least
minimize, the overlapping of the tape and tow junction (chimney effect)
that would locally reduce the material strength. This is done by
defining precisely an origin point for tooling each ply through
staggering.
Top view of plies without staggering:
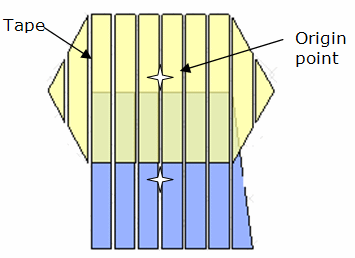
- Top view of the same plies with staggering:

- Front view of the same plies, first without staggering, then with
staggering:

Define Stagger Origin Points generates stagger origin
points for each ply and checks validity of existing ones.
The Origin point is the starting point used to tool a ply. Stagger
origin points avoid the overlapping of tapes or tows junction.
The Reference point is the point used to generate stagger origin
points, generally the origin of the rosette.
The output will be:
- The origin point for each ply,
- Analysis results and reason when KO,
- Viewer in the suggested UI,
- An exported table containing the stagger indexes and warning
messages.
|
|
-
Click Define Stagger Origin Points
.
The Stagger Origin dialog box is displayed:

-
Select the Plies group to process.
The dialog box is populated with information gathered from this Plies group.
 This Plies group is divided into Homogeneous sets i.e.
sets of plies that share the same rosette, the same valid orientation,
the same reference point and share a common area of the reference
surface with another ply of the set.

They are listed by their index in the second column (Homogeneous
set).
Two plies that share the same common area are linked.
Filters are now available, based on the Homogeneous sets, Rosette,
Reference point and Orientation of the plies.
Selecting a line in the dialog box highlights the corresponding ply in
the 3D window.
Here, filter has been applied on Homogeneous set 4 and a few plies have
been selected:

-
Click COMPUTE. Stagger origin points are
computed.
When the computation is done, select a ply in the dialog box.
It is highlighted in the 3D Window:

For stagger index =0:
- Starting from a reference point, a geodesic line is
created on reference surface using fibber orientation (e.g.
-45 degrees) given by rosette transfer.
- Geodesic curves parallel to previous reference curve are
created on surface with a geodesic distance equals to
Material Width plus Gap. Those
parallels are extrapolated up to the surface limits if
needed.
- Intersection of these parallels with Ply.14 (rectangle
in fat pink) are computed.
- Segment for origin point (solid pink line) is defined as
the centered intersection.
- Origin point is the middle of this segment.
For the following indices, the same computation is applied,
but the first parallel is offset by a distance equal to the
Minimum Staggering Value.
 |
-
In the dialog box, information is given on the
computation:

-
Modify the Parameters and restart the
computation. The status and the diagnostic list displayed at the end of
the computation helps you modify these parameters.
- Stagger index, i.e. the integer value associated to a
ply to define the position of its origin point with respect
to the reference point:
- with minimum stagger indices: only
minimum stagger indices are used, i.e. 0 and 1.
- with maximum stagger indices: more
stagger indices can be used. Tip: they are listed under
the Homogeneous set column.
- Note that two linked plies cannot have the same
index.
- Minimum Stagger Value (MSV): distance between two stagger
indices to get optimum shear strength. The default value is 20mm.
- Width: width of the material, i.e. tape width.
The default value is 100 mm.
- Gap: value of the gap that exists between two
adjacent tapes.
- Minimum nb plies: minimum number of plies that must
be located between two plies with the same stagger value in the same
homogeneous set of plies. The default value is 4.
- Tolerance: maximum distance between manual origin point
and stagger origin point computed from the stagger index.
|
-
Select one or several plies in the dialog box. Point
management become available:

- Place your cursor in Reference and select a
point in the 3D window or the specification tree to replace
the current reference point of the plies selected.
- The modification will apply to all the plies
selected.
- Click reset default to revert to the
default reference point, that is the origin of the ply
rosette.
- Place your cursor in Origin and select a
point in the 3D window or the specification tree to replace
the current origin point of the plies selected.
- The modification will apply to all the plies
selected.
- A confirmation is requested to change the parent
body if the point selected does not belong to the open
body MANUFACTURING of the ply. This confirmation is
requested for each ply selected.
- Click reset as computed to revert to the
computed origin point.
- Modify from Stagger index provides a
drop-down list of the indices used for the computation of
stagger origin points. Select one index to change the
current one.
- When one ply only is selected, the drop-down list
proposes only the indices that will not lead to an
error, while all values are proposed when several plies
have been selected.
- A confirmation to change the Origin is
requested when you select a new index.
|
-
If required, click Export table... to export the result
as a file.

-
Click OK when done to validate and exit the
dialog box. The stagger origin point is created under the ply.
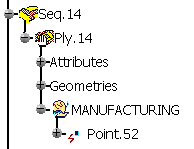
-
When stagger origin points already exist in a plies
group, start the command and click Check to check their
validity.
You can then edit them as explained above.
|