|
This task
shows how to create a Seam Welding Connection Property between two parts or
within one part.
A Seam Welding Connection Property is a connection that is
created from an existing Line Analysis Connection or Line Analysis
Connection Within One Part. |
 |
Only available with the Generative Assembly Structural
Analysis (GAS) product. |
 |
|
 |
-
Click Seam Welding Connection Property
in the Connection Properties toolbar.
The Seam Welding Connection Property dialog box
appears.

|
 |
-
If you select the Shell, Hexahedron,
Spring-Rigid-Spring, Rigid-Spring-Rigid,
Contact or Beam option type, the Component
edition button appears
.
-
The Component edition button can have
two status:
-
valid:

-
invalid:

-
If you select Shell, Beam or
Hexahedron option type, you can select a user-defined
material.

For more details, refer Creating User
Materials.
|
-
Select the seam welding connection.
In this particular example, select Line Analysis
Connection.1 in the specification tree.
 |
-
Select the desired Type option.
In this particular example, select Shell. |
-
Click the Component edition button
to specify the parameters.
The Seam Welding Definition dialog box appears.
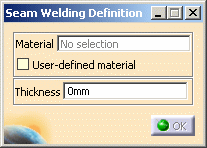
-
Material: gives you information about
the associated material.
-
User-defined material: lets you select
an user material.
For more details, refer Creating an User
Material.
-
Thickness: lets you specify a thickness
value.
|
-
Specify the desired parameters.
In this particular example:
-
Click the User Defined Isotropic Material
check box.
-
Click the Material text box.
-
Select the User Isotropic Material.1
object in the specification tree.
-
Enter 1mm as Thickness value.
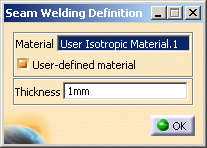 |
-
Click OK in the Seam Welding Definition dialog
box.
Note that the Component Edition icon
becomes valid.
 |
-
Click OK in the Seam Welding Connection
Property dialog box.
A Seam Welding Connection Property.1
connection property appears in the specification tree under the
Properties.1 set and a Weld Seam Connection Mesh.1
connection mesh part appears under the Nodes and Elements
set.
 |
|
 |
|
|
 |
The weld seam connection mesh part is created with a
default Step value.
This value is computed as a ratio of the seam length.
In case this value is much smaller than the size of
the connected meshes, the size of the problem to be solved is
considerably increased. This may lead to an "Out of Memory" error.
You can find here a recommended methodology to avoid
this error:
-
Create the Seam Welding Connection Property.
-
Edit the Seam Welding Connection Mesh
part in the specification tree.
-
Check that the Step value respects the
proportion of the connected meshes (commonly used value: half of
the smallest connected mesh).
-
Launch the computation.
|
|
|

|
 |