 |
Connections |
Support |
Analysis Connections (from R12)
Point Analysis Connection
Point Analysis Connection within one Part |
One or two |
Body in White Fastener Connections
Joint (containing or not hemming information) |
One or more |
Analysis Connections (before R12)
Spot Welding Analysis Connection |
Two |
For more details about analysis connections, refer to the
Generative Structural Analysis User's Guide -
Analysis Connections.
For more details about joint containing hemming
information, refer to the Automotive Body in White Fastening User's
Guide - Creating Joint Bodies. |
 |
-
Click Spot Welding Connection Mesh
in the Welding Meshing Methods toolbar.
The Spot Welding Connection Mesh dialog box appears.
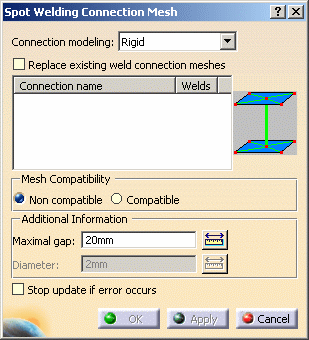
- Connection modeling:
- Replace existing weld connection meshes: allows you
to select a weld spot connection that has been already associated
to a mesh part.
 |
You must activate this option before selecting
the weld spot connection.
If not, a warning message informs you that the weld spot
connection has been already meshed. |
- Mesh Compatibility:
- Non compatible: lets you create nodes by
orthogonal projection of the welding points on the two mesh
parts.
- Compatible: lets you use existing nodes.
- Additional Information:
- Maximal gap: lets you specify the radius value of
a sphere which has the welding spot as center. It must be an
intersection between each face and the solid thus defined.
 |
- The value must be strictly positive.
- While the Maximal gap value is null, the
OK and the Apply buttons will be not
available.
- If you update spot welding connections created before
the V5R12 level without modifying them, the data used to
mesh are the same as those used up to the V5R11 level.
Errors could be generated (for example: the maximal gap
value is too small).
In this case, you have to edit the connection mesh and to
increase the Maximal Gap value.
|
- Diameter: lets you specify the diameter of the
hexahedron.
 |
This option is only available if you selected
the Hexahedron and the Non compatible
options. |
- Stop update if error occurs: lets you stop the
Update all meshes process.
If this option is activated and if you use the Update all
meshes contextual menu, only the meshes created before the
weld spot connection mesh will be updated.
|
-
Select the connection you want to mesh in the
specification tree.
In this particular example, select the Point
Analysis Connection.1 object in the specification tree (under
the Analysis Connections Manager.1 set).
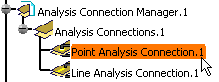
The Spot Welding Connection Mesh dialog box is
updated.
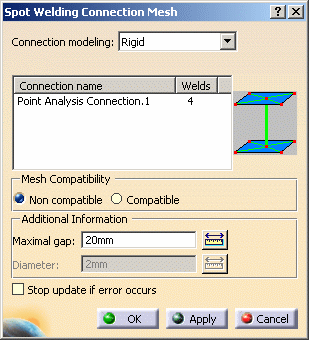 |
-
Set the desired parameters.
In this particular example:
-
Select Beam as Connection modeling
option.
-
Select Non compatible as Mesh
Compatibility option.
-
Enter 2mm as Maximal gap
value.
|
-
Click Apply.
Several errors are displayed in the specification
tree under the Spot Welding Connection Mesh.1 object.
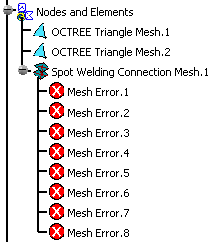
You have to change the Maximal gap value. |
-
Enter 5mm as Maximal gap value.
-
Click Apply and then OK.
The connection mesh is now correct.
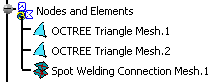 |
 |
For a better visualization, you can change the mesh
color using the Properties contextual menu.
You can also hide the OCTREE Triangle Mesh.1
and OCTREE Triangle Mesh.2 using the Hide/Show
contextual menu:
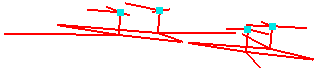 |
-
Change the weld spot connection mesh parameters.
To do this, double-click the Spot Welding
Connection Mesh.1 object in the specification tree to edit it.
The Spot Welding Connection Mesh dialog box appears.
In this particular example:
-
Select Hexahedron as Connection
modeling option.
-
Enter 3mm as Diameter value.
-
Click Apply and then OK.
If you use the Hide/Show contextual menu
to hide the OCTREE Triangle meshes, the result will be:
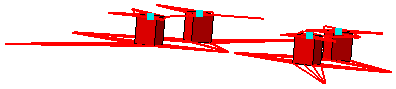 |
|