Multi-Slide Lathe Machine
This section deals with the multi-slide lathe machine that is available when
the Multi-Slide Lathe Machining add-on product is installed in the Lathe Machining
workbench. It describes:
Machine Capabilities for the Multi-Slide Lathe
Machine
Multi-slide lathe machine comprises a number of spindles and turrets, which you
specify in the Machine editor dialog box.
In the Turret and Spindle tabs of this dialog box, the presentation is similar:
- On the left, the list of turrets and spindles with command buttons to add
or remove these entities.
There must always be a minimum of one turret and one spindle.
- On the right, properties of the selected element are displayed.
Note that addition of turrets and spindles is only possible when Multi-Slide
Lathe Machining is installed.
Turret Definition
Here is an example of the Machine Editor's Turret tab:

Each turret has a name, which will be displayed in the PPR tree next to the program
with which it is associated.
Each turret has a number, which is output in APT output in place of MFG_CHANNEL_NUMBER
in the program header or synchronization syntax.
You can specify the Turning Tool Axis System by clicking
in the dialog box.

The Axial and Radial axes of this axis system define the working plane of the
turret for turning operations: tool path, replay, and time based replay are represented
in this plane.
This axis system can be any axis system. However, the working plane must contain
the spindle axis that the turret works on.
At the bottom of the Turning Tool Axis System dialog box:
- The angle defines the incline of the Turret Plane with respect to the ZX
plane of the first spindle (that is, the Setup axis system).
- Radial and axial shift give the position of the origin of the axis system
relative to the origin of the first spindle (that is, the origin of the Setup
axis system).
For more information, see Axis Systems for Part and
Turning Tool.
Tool Change point can be defined manually through its absolute coordinates (X,Y,Z).
Since this point might be considered as the origin of the Turning Tool Axis System,
you can use the button at the bottom of the Machine Editor to automatically set
it.
Spindle Definition
Here is an example of the Machine Editor's Spindle tab:

Each spindle has a name, which will be displayed at the bottom of operation editor.
Note that this is the case when there is more than one spindle on the machine. Otherwise
the single spindle is used by default. It is output in APT in place of MFG_SPINDLE_NAME.
Each spindle has a number, which is written in valuated in APT in place of MFG_SPINDLE_NUMBER.
Spindle name and number can be valuated in NC_MACHINING_AXIS and NC_ACTIVITY_HEADER
syntaxes .
Part Axis System defines the plane where tool path, replay, and time based replay
are represented.
For more information, see Axis Systems for Part and Turning
Tool.
Maximum Spindle Speed is taken into account for time computation in Machining
Gantt Chart.
Counter Spindle Output
Counter spindle output is managed by the Use Spindle Axis system according
to the Spindle involved on the Machining Operation checkbox in the Option
tab of the Part Operation editor. This is for a Multi-slide lathe machine or a Mill-Turn
machine.
- If this check box is selected, tool tip points are computed based on the
spindle that is set on the machining operation.
- If this check box is not selected, the main spindle axis is used. This is
determined by the default reference machining axis system set on the Part Operation.
Note: To get the tool path points with respect to Counter Spindle Part axis
system, a workaround consists of having a Machining axis system on the Counter
Spindle Part axis system.
Example of Using Spindle Axis System According to the Spindle on the Machining
Operation
This option provides tool path points or coordinates of the tool positions of
the tool path for machining operations defined on the Counter Spindle with respect
to Counter Spindle Part axis system. Machining Axis change definition is avoided.
Here is a view of the Multi-Slide Lathe Machine setup showing main and counter
spindles:

A program is defined with one machining operation defined on the main spindle,
and a second operation on the counter spindle:
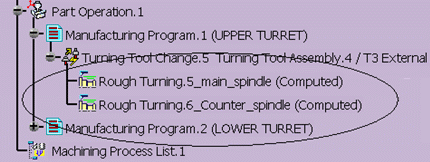
The counter spindle is set on the second operation:

Replay of the machining operation defined on the counter spindle:

Sample of the APT output obtained for the program:
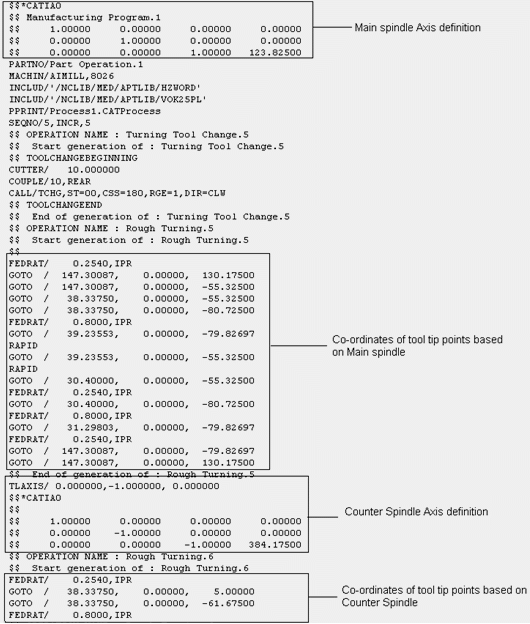
Other Counter Spindle Capabilities
The following counter spindle capabilities are introduced in V5R19:
- Prior to V5R19, Counter Spindle Axial axis needed to be parallel to Main
Spindle Axial axis.
Counter Spindle can now be defined at any angle to Main Spindle axis.
- Prior to V5R19, the tool path could not be located in the Turret plane if
the Counter Spindle Part axis system was rotated by an angle (that is, if Counter
Spindle plane was not at zero degrees). Now the tool path on the Counter Spindle
is in Turret plane.
Resource Attributes for the Multi-Slide Lathe Machine
The Multi-Slide Lathe Machine (CATEMfgMultiTurretLatheMachine) resource attributes
are described below.
Base Attributes
These attributes provide general information.
MFG_NAME (Name)
Type: String
Specifies the name of the resource. |
MFG_COMMENT (Comment)
Type: String
Associates a comment to the resource. |
Numerical Control Attributes
These attributes characterize the machine controller and have an impact on the
output format.
MFG_PP_WORD_TBL
(Post Processor words table)
Type: String
Specifies the name of the PP words table which is used for creating
Post Processor word syntaxes. |
MFG_OUTPUT_TYPE
(NC data type)
Type: String
Possible values:
APT
CLF-3000
CLF-15000
ISO
Specifies the type of NC data output by the application. It can take
the following values: APT (APT source, this is the default), CLF-3000
(clfile record types 3000 and 5000 are output), CLF-15000 (clfile record
type 15000 is output), ISO. |
MFG_OUTPUT_FRMT
(NC data format)
Type: String
Possible values:
POINT (Point (X,Y,Z))
AXIS (Axis (X,Y,Z,I,J,K))
Specifies the format of the NC data output. It can take the following
values: POINT (X,Y,Z point coordinates, by default), AXIS (X,Y,Z,I,J,K
point coordinates and tool axis components). |
MFG_STRT_PT_SYNT
(Home point strategy)
Type: String
Possible values:
FROM (FROM)
GOTO (GOTO)
Specifies the type of trajectory on the start point: GOTO or FROM
|
MFG_MAX_FEEDRATE
(Max machining feedrate)
Type: Real
Specifies the maximum machining feedrate. This is used in NC Manufacturing
Verification Product Errors (tool collision with the stock) will be
reported if the feedrate exceeds this value |
MFG_RAPID_FEED
(Rapid feedrate)
Type: Real
Specifies the rapid feedrate. This is used to compute the total machining
time and may replace the RAPID instruction in output APT files. |
MFG_AXIAL_RADIAL_MOVE
(Axial/Radial movement)
Type: Boolean (Yes/No)
Specifies the ability to generate automatically axial and radial movements
to avoid collisions in axial operations |
MFG_INT_LIN_3D
(3D linear interpol.)
Type: Boolean (Yes/No)
Specifies if the machine is able to make a 3D linear interpolation between
2 points. |
MFG_INT_CIRC_2D
(2D circular interpol.)
Type: Boolean (Yes/No)
Specifies if the machine is able to make a 2D circular interpolation
between 2 points. |
MFG_INT_CIRC_3D
(3D circular interpol.)
Type: Boolean (Yes/No)
Specifies if the machine is able to make a 3D circular interpolation
between 2 points. |
MFG_R_MIN_CIRC
(Min interpol. radius)
Type: Real
Specifies the minimum radius of circular interpolation that the machine
is able to achieve. |
MFG_R_MAX_CIRC
(Max interpol. radius)
Type: Real
Specifies the maximum radius of circular interpolation that the machine
is able to achieve. |
MFG_MIN_DISC (Min
discretization step)
Type: Real
Specifies the minimum distance between two consecutive points that the
machine is able to achieve.Note:
The application compares the minimum discretization step and the machining
tolerance. The larger of the two values is taken to be the minimum distance
between two points.
When you generate NC data, any points that are spaced at a distance
less than this value are eliminated from the output file.
|
MFG_MIN_ANGLE
(Min discretization angle)
Type: Real
Specifies minimum angle between tool axis at two consecutive points
that the machine is able to achieve. The application eliminates points
whose tool axis orientation does not meet this criteria. |
Spindle Attributes
These attributes provide information on the spindle and have an impact on spindle
capabilities.
MfgLmtSpindleName (Spindle
name)
Defines the name of the spindle, output in NC code.
|
MfgLmtSpindleNumber
(Spindle number)
Defines the number of the spindle, output in NC code.
|
PAS (Part axis system)
Defines the Part axis system on a spindle.
|
MFG_LATHE_RAD_AX
(Radial axis)
Type: String
Possible values:
X
Y
Z
Defines the radial axis, which is generally the X axis.
Combined with the spindle axis, it defines the programming working plane,
where the selected geometry is projected. |
MFG_LATHE_SPN_AX
(Spindle axis)
Type: String
Possible values:
X
Y
Z
Defines the spindle and C axes, which is generally the Z axis.
Combined with the radial axis, it defines the programming working plane
where the selected geometry is projected. |
MFG_LATHE_MAX_SPNDL_SPEED
(Max spindle speed)
Type: Real
Defines the maximum speed of the spindle. It is used in time
computations when machining at constant cutting speed. |
Turret Attributes
These attributes provide information on the turret definition and have an impact
on turret capabilities.
MfgLmtTurretName (Turret
name)
Defines the name of the turret, output in NC code.
|
MfgLmtTurretNumber (Turret
number)
Defines the number of the turret, output in NC code.
|
Turret type
Defines the turret type as:
- Rotary Turret (default setting)
- Mill Turret, turret that has B-axis capability.
|
TAS (Turning Tool axis
system)
Defines the Turning Tool axis system on a turret.
|
MFG_LATHE_RAD_AX
(Radial axis)
Type: String
Possible values:
X
Y
Z
For a given turret, it defines the radial axis of the Turning Tool axis
system, which is generally the X axis.
Combined with the axial axis, it defines the plane where Turning tooling
is represented. |
MFG_LATHE_AX_AX
(Axial axis)
Type: String
Possible values:
X
Y
Z
Defines the axial axis of the Turning Tool axis system, which is generally
the Z axis.
Combined with the radial axis, it defines the plane where Turning tooling
is represented. |
MFG_X_TOOL_POS (Tool
change point X)
Defines the X coordinate of the tool change point with respect to the
reference machining axis system. |
MFG_Y_TOOL_POS (Tool
change point Y)
Defines the Y coordinate of the tool change point with respect to the
reference machining axis system. |
MFG_Z_TOOL_POS (Tool
change point Z)
Defines the Z coordinate of the tool change point with respect to the
reference machining axis system. |