|
|
 |
|
 |
-
-
-
|
-
|
|
|
-
|
-
|
-
-
|
-
-
-
|
-
-
-
|
-
|
 |
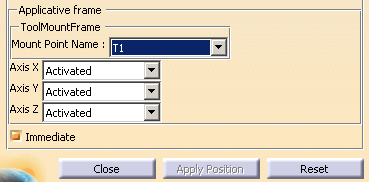
|
 |
|
|
Modifying Workpiece and Tool Mount nodes
under the NC Controller
|
 |
Open the
V4Axis_Machine.CATProduct file. In addition:
|
 |
-
On the specification tree, select Workpiece Mount
Point.
 |
The system prompts you to select a part. |
-
On the specification tree, select CTable.
The corresponding geometry in the graphics area gets highlighted.
The green compass is also positioned at the origin of the machine. |
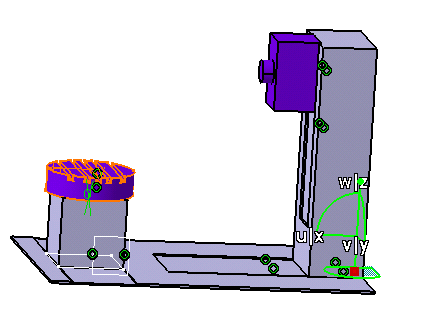 |
The Set Location dialog box appears. |
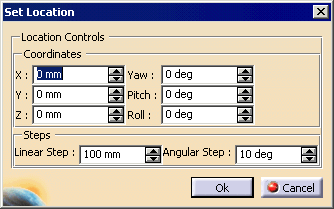 |
-
Use the red center of the compass to drag and drop it on
the selected CTable product, or use the above dialog box to
position the compass on the selected workpiece mount part.
-
Click OK.
The CTable is now the workpiece mount part with the
point described in the Set Location dialog box set to the workpiece
mount point.
You can modify this location at any time by repeating
the above procedure. |
-
Repeat the above steps, for Tool Mount Point, selecting ZAxis
instead of CTable.
The ZAxis is now the tool mount part, with
the point described in the Set Location dialog box, set to the tool
mount point.
You can modify this location at any time by repeating
the above procedure. |
-
Jog the machine to validate the automatically assigned
inverse kinematics solver, by clicking Jog Mechanism .
|