 |
This task shows you how to analyze the producibility,
that is to simulate the fibers behavior of a ply in order to
detect manufacturability problems.
Within this command you can also:
|
 |
Available in Composites Engineering
Design (CPE) and Composites Design for Manufacturing
(CPM). |
 |
Open the
Producibility1.CATPart
document. |

|
-
Click the Producibility icon
in the Flattening toolbar.
The Producibility dialog box is displayed.

-
Select a ply in the specification tree. Note that multi-selection of plies is possible.
In our scenario, we have selected Ply.1.
The Warn angle and
Limit angle
values are automatically displayed.

The reference angle is 90 degrees.
-
The
Warn angle defines the maximum deformation and
must be +/- 15
degrees according to the reference angle.
-
The
Limit angle defines the limit deformation and
must be +/- 30
degrees according to the reference angle.
A color code applies depending on the deformation
values:
-
blue: the
deformation is lower than 15 degrees according to the reference
angle,
-
yellow: the
deformation is between 15 and 30 degrees according to the reference
angle,
-
red: the
deformation is higher than 30 degrees according to the reference
angle.
|
-
In the
Seed Point field,

select the seed (strategy)
point,
that is the point used to start the circular propagation of the
fibers.
The original fiber directions are displayed on the point
(blue for warp and red for weft)
and the dart creation becomes available.

Two methods are available to select the seed point:
- Point selection:
you select an existing GSD point.
Should you need to create the seed point,
right-click in the Seed Point field and create the element you
need.

Refer to Generative Shape Design & Optimizer User's Guide
for more information. |
 |
This point must be selected within the external contour of
the ply and lie on the surface. |
- Point
indication: you pick a point, existing or not
(i.e. you
simply pick where you would create a seed point),
within the
boundaries of the selected ply.
This allows you a quicker analysis of the producibility as you can
restart
the analysis with another point without creating an existing
point.
- Both mode enables you to store the producibility
parameters in the model when you click OK.
|
-
Define the
Warp and
Weft values for
the fibers meshes.

In our scenario we selected 10mm..
-
Warp:
radius used to simulate the fibers behavior along the X direction.
-
Weft:
radius used to simulate the fibers behavior along the Y direction.
The lower the radius values are, the more precise the
meshes will be. |
-
Select the
propagation type from the list:

-
Minimum
distortion: deformation computed by the system so as to
minimize the distortion.
-
Symmetric: deformation computed symmetrically regarding the
fiber direction.
The system forces the propagation to be
symmetrical.
|
-
Select the
With thickness update check box and then the option
you need to compute the thickness of plies:
-
Core
sampling range: enter the required depth of the core sampling.
-
Full
stacking: to use when the groups of plies are defined on the
same reference shell.
-
Ply
group only: to use when groups of plies are defined on various
shells,
as each shell takes into account the plies defined under a
group.
|
 |
You can leave the default value in the Core sampling range field, yet,
make sure the size of the core sampling will not make it go right
through the part if it is in U shape for instance. |
-
Click Apply to run the analysis and start the
simulation.
Fiber meshes display in the 3D geometry.
 |
Minimum Distortion |
In the above picture, the shape of the surface is not
symmetrical.
On this non-symmetrical shape, the fiber propagation with
the "minimum distortion"
option follows the curvatures of the surface
while minimizing the deformation of the fibers. |
 |
Symmetric |
With the "symmetric" option, the system forces the
fiber propagation to be symmetrical. |
-
Click More to display the
Analysis display mode
parameters.

By default, the
Deformation option is selected.
The analysis is based on the angle between the fiber meshes.
-
Select the
Deviation option.
When using this option, the rosette is transferred at each point of the
fiber mesh.
The analysis is based on the delta between the theoretical and
the actual fiber angles of each point.
-
Enter values for the Warn Angle and the
Limit Angle and click Apply to start the analysis.
The simulation is displayed in the 3D geometry.
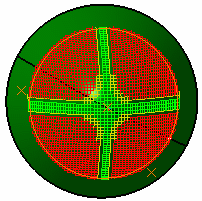 |
The reference angle is 0 degree.
-
The
Warn angle defines the maximum deformation and
must be +/- 5
degrees according to the reference angle.
-
The
Limit angle defines the limit deformation and
must be +/- 10
degrees according to the reference angle.
A color code applies depending on the deviation
values:
-
green: the
deviation is lower than 5 degrees according to the reference angle,
-
yellow: the
deviation is between 5 and 10 degrees according to the reference
angle,
-
red: the
deviation is higher than 10 degrees according to the reference
angle.
|
-
Click
Keep.

The curves
generated by the producibility
analysis are stored in a geometrical set.
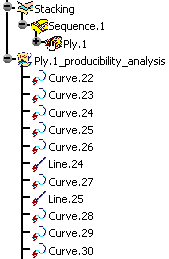
You can rely on those curves if you later want to create a
dart or a splice in order
to lower the ply deformation.
Use the inspection points to create the limiting
or splicing curves.

|
 |
- We advise you to delete the
geometrical set containing the producibility curves
once you have created
your limiting or splicing curves, as it will ease the processing of your
model.
- Make sure you create the limiting or splicing curves as data, in
order not to delete
them with the producibility curves.
|
|
-
Click
Inspection to start the
inspection of the producibility on the
selected ply.
Note that the operating mode is the same as with the Producilibilty
Inspection icon,
less the Create file from fields, as they are not necessary here.
-
Click OK to create a producibility parameters
feature under the ply in the specification tree.
Parameters (i.e. seed point, warp and weft) are now stored and
may be
later used when flattening plies.

|
 |
If several plies are selected,
Apply is dimmed.
Therefore OK creates one producibility
parameters feature under each selected ply. |
 |
Computation might detect an error
when analyzing the producibility of plies.
In that case, a warning is
displayed to advice you to modify the fiber simulation strategy. |
|
Displaying the Flat Pattern
-
Select the Display Flat Pattern check box to
preview the flatten shape of the ply or of the cut-piece to be displayed
in the 3D viewer.

-
Click Apply to preview the flatten shape.
The seed point and the x and y axes of the rosette transferred at this seed
point define the plane in which the flatten shape is positioned.

|
|
The Check Material Width check box becomes available once you
have selected Display Flat Pattern.
-
Select the Check Material Width check box to
determine whether a ply or a cut-piece geometry fits into the given
material width.

This is done as follows:
Two lines representing the material roll sides are displayed on the flat
pattern of the ply.
The first line is positioned at the extremity of the flat pattern.
If the second line intersects the flat pattern, a warning is displayed.
If the flat pattern is larger than twice the material roll width,
additional lines are displayed.

-
You can choose to check the material width along:
-
the warp: the lines are perpendicular to the blue line of the
transferred rosette,
-
or along the weft: the lines are perpendicular to the red line of the
transferred rosette.
-
switching from one option to the other rotates the lines by 90 degrees.
|
-
Click Apply. A green or a red sign is displayed to indicate
whether
the flatten shape fits into the material roll width or not.
or
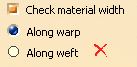
|
|
-
Once an entity and a point have been selected, the
button becomes available.
It starts the Dart
command and deactivates temporarily the Producibility
command.
-
Once you are done with the dart creation, you will
revert to the Producibility dialog box.
|
 |